Plastic extrusion for tubing, sections, and custom shapes
Plastic extrusion for tubing, sections, and custom shapes
Blog Article
Key Advantages and Factors To Consider of Applying Plastic Extrusion in Your Projects

Comprehending the Essentials of Plastic Extrusion
Plastic extrusion, a staple in the production sector, is a procedure that includes melting raw plastic product and reshaping it into a constant profile. This profile, as soon as cooled down, can be reduced into wanted lengths or curled for later use. The elegance of plastic extrusion exists in its convenience. A large range of products, from piping to home window structures, can be generated. The procedure needs an extruder, a detailed device with a warmed barrel, a turning screw, and a die at the end. The plastic material, in the kind of pellets, is fed into the extruder, where it's thawed and forced through the die, taking its shape. The option of plastic and the style of the die identify the product's attributes.
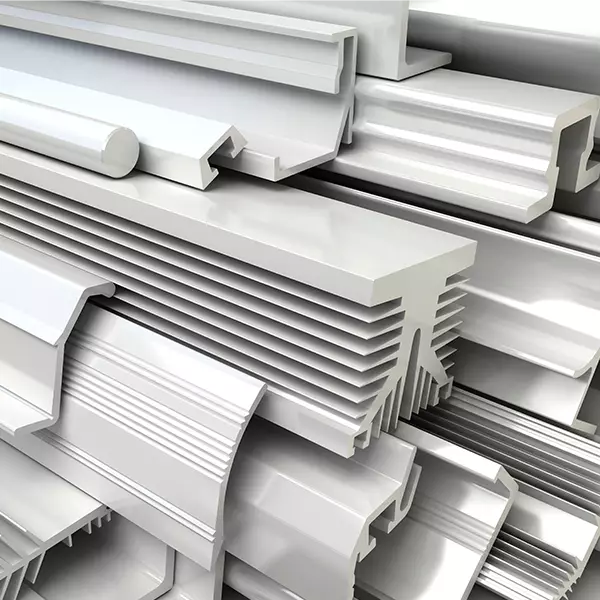
The Economic Advantage of Plastic Extrusion
The economic advantage of plastic extrusion lies mainly in 2 areas: affordable material production and beneficial production speeds. With plastic extrusion, services can create high volumes of product at a lower price contrasted to various other techniques. The procedure boasts a remarkable production rate, dramatically lowering time and more enhancing its financial viability.
Affordable Material Manufacturing
A considerable advantage of plastic extrusion is its exceptional cost-effectiveness. In addition, the extrusion process enables for a high level of accuracy in shaping the plastic, lowering the need for expensive post-production changes or adjustments. All these elements make plastic extrusion a very cost-effective choice for numerous tasks, using an attractive balance in between expense and efficiency.
Beneficial Manufacturing Speeds
While maintaining the cost-effectiveness of the materials, an additional significant advantage of plastic extrusion lies in its quick manufacturing rates. This efficiency in the manufacturing procedure is credited to the constant nature of the extrusion process, enabling high-volume manufacturing in a reasonably short time period. The rate of manufacturing directly associates to a decline in labor expenses and an increase in result, consequently improving the general financial practicality of the process. Additionally, the busy manufacturing does not compromise the high quality of the last product, making certain reputable and constant results. This mix of cost-effectiveness, quality, and rate emphasizes the considerable financial benefit of executing plastic extrusion in numerous tasks.
Convenience and Customization: The Toughness of Plastic Extrusion
Among the prominent toughness of plastic extrusion depends on its flexibility and personalization potential. These qualities unlock to limitless layout opportunities, providing suppliers the capacity to tailor items to certain requirements. This heightened level pop over here of modification not only improves product performance but also significantly boosts item originality.
Unrestricted Style Possibilities
Plastic extrusion radiates in its capability to provide nearly unlimited layout opportunities. This technique supplies liberty to develop intricate forms and intricate accounts, a feat difficult to achieve with various other manufacture strategies. Owing to the fluid nature of molten plastic, the process is versatile enough to yield a varied series of dimensions, dimensions, and types. The plastic can be adjusted to match one-of-a-kind specifications, enabling for the manufacturing of customized geometries and meeting specific client demands. Plastic extrusion can handle a variety of plastic kinds, expanding its application scope. This adaptable method, therefore, serves a vast array of industries from building and construction to automotive, product packaging to electronic devices, and beyond. With plastic extrusion, the style opportunities are basically countless.
Improving Item Originality
The versatility of plastic extrusion can considerably boost product originality. This procedure allows designers to explore different forms, sizes, and colors, providing them the freedom to create one-of-a-kind items that attract attention out there. It is this personalization that provides a distinctive identification per item, distinguishing it from its competitors.
Along with its visual benefits, the customizability of plastic extrusion likewise provides useful benefits. Designers can customize the homes of the plastic according to the specific needs of the application, enhancing the item's functionality. As an example, they can make the plastic a lot more flexible, a lot more durable, or a lot more resistant to heat, depending upon what the product requires. Hence, plastic extrusion not just increases product individuality yet additionally its utility and bankability.
Style Limitations in Plastic Extrusion: What You Required to Know
Just how can design restrictions possibly impact the process of plastic extrusion? While plastic extrusion is flexible, design restrictions can stop its advantages. Comprehending these constraints is important for effective implementation of plastic extrusion in your jobs.
Assessing the Ecological Impact of Plastic Extrusion
While comprehending style restrictions is a significant facet of plastic extrusion, it is similarly crucial to consider its environmental implications. The process of plastic extrusion entails melting plastic products, potentially releasing damaging gases right into the environment. Using recycled plastic materials in the extrusion process can decrease ecological impact.

Study: Effective Projects Making Use Of Plastic Extrusion
Success stories in the field of plastic extrusion abound, showing both the convenience and effectiveness of this production procedure. plastic extrusion. Another successful instance check over here is the manufacturing websites of plastic movie for packaging and farming. These circumstances illustrate plastic extrusion's critical duty in different sectors, proving to its versatility, cost-effectiveness, and dependable result.
Conclusion
To conclude, plastic extrusion offers a efficient and cost-effective technique for generating complex forms with minimal waste. While it provides many benefits such as cost-effectiveness and flexibility, it's important to take into consideration prospective style restrictions and environmental effects. Applying biodegradable or recycled materials can minimize these issues, improving sustainability. Integrating plastic extrusion into jobs can cause successful results, as shown by many study.
Plastic extrusion, a staple in the production sector, is a process that involves melting raw plastic material and improving it right into a constant account. Plastic extrusion can deal with a selection of plastic types, broadening its application extent.Just how can design restrictions possibly affect the procedure of plastic extrusion? The procedure of plastic extrusion involves melting plastic products, possibly releasing dangerous gases right into the environment. Utilizing recycled plastic products in the extrusion process can reduce environmental impact.
Report this page